Liquid Hydrogen - Air Travel's Future Fuel?
- Jan 3, 2020
- 3 min read
There has always been a special concern about high energy fuels. To understand why, it is fundamental to understand what 'Specific Energy' is. Specific Energy (measured in MJ/kg) is the energy per unit mass, namely the amount of energy that we can obtain from burning 1 kg of fuel. For example, if we burn the same quantity of 2 fuels with 2 different values of specific energy, we will get a different amount of energy. It's easy to see why in aviation, it is important to always choose the higher energy fuel, to save weight or to save money, by using less quantity of fuel and obtaining the same engine performances. The best fuel is the one that has the highest energy to weight ratio.
The list of the high energy fuels is not so long, but just to mention some, Kerosene (46.2 MJ/kg), Gasoline (46 MJ/kg), and Methane (55.5 MJ/kg) are among the most high energy fuels available today. On top of the list, there is liquid Hydrogen (141.8 MJ/kg) that unfortunately was made famous by the Hindenburg disaster in 1937.

A Difficult Start
Despite the Hindenburg disaster, there was renewed interest in liquid hydrogen in the 1950s. It was still a very difficult fuel to handle due to its flammability, but the American National Advisory Committee for Aeronautics (NACA) focused its resources on this project, intending to use it for high altitude aircraft. It was discovered that it worked very well in turbojet engines at an altitude of 30 km (100,000 ft) at which traditional fuels failed. The thrust was also about 5% higher and the fuel consumption was about 70% lower.
In 1956 NACA started Project Bee, which used a converted Martin B-57 Canberra Bomber to test liquid hydrogen fuel tanks at sea level and high altitudes. The engines onboard the plane could switch between traditional fuel and liquid hydrogen with ease, showing that hydrogen left a dense contrail because the exhaust was almost entirely water vapor, while the traditional fuel left no such visible contrail.
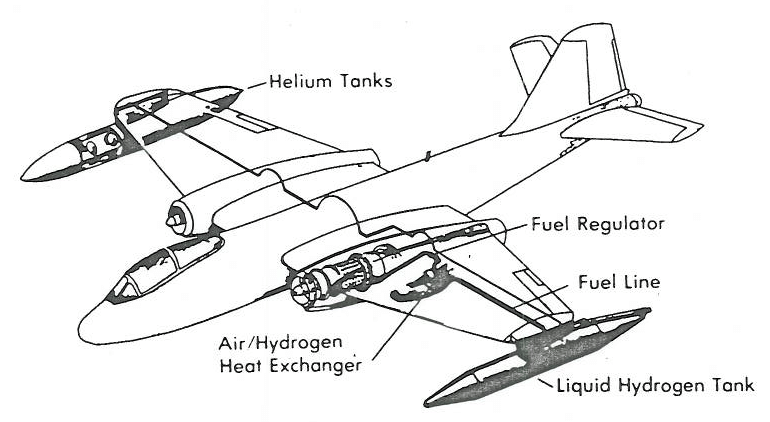
Why Didn't We Switch To Hydrogen Fuel?
The biggest obstacles to using hydrogen in the aviation industry are:
1.Its high flammability
2.Its difficulty in handling
3.Its rarity in pure form
Hydrogen possesses the NFPA's (Standard System for the Identification of the Hazards of Materials for Emergency Response) highest rating on the flammability scale because it is flammable when mixed even in small amounts with ordinary air. The storage and use of hydrogen pose unique challenges due to its ease of leaking as a gaseous fuel and its ability to embrittle metals that must be accounted for to ensure safe operation. It has to be kept as a liquid by cooling it to -252 °C in very special cryogenic tanks with thermal isolation. Finally, because of its rarity in nature, it has to be created in laboratories, breaking larger molecules such as water (H2O) and hydrocarbons to release the hydrogen within, which is a very high energy-intensive process.
In comparison with Kerosene, today's most used jet fuel, with a density of 800 kg/m3, Hydrogen has a density of 71 kg/m3 which is a huge advantage in terms of weight, allowing the possibility of building smaller fuel tanks and improving the aerodynamics of the airframe. NASA is currently working on electric planes with improved aerodynamics, powered by liquid hydrogen, eventually making the use of hydrogen a cost-effective choice in the future.
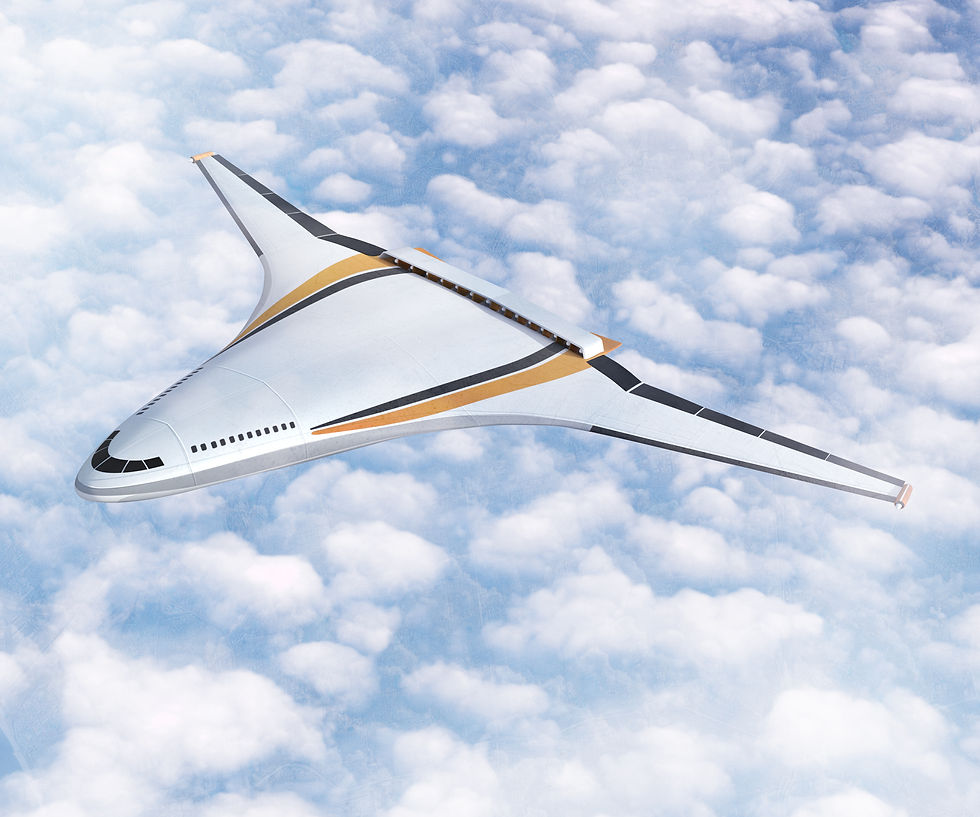
Nowadays, the cost of making Hydrogen is still too high compared to the relatively cheap cost of oil. It would take a big change in political decisions, oriented towards a greener aviation environment, to see these costs go down. We may never see a completely liquid hydrogen-powered airliner but we cannot ignore its potential.
Comments